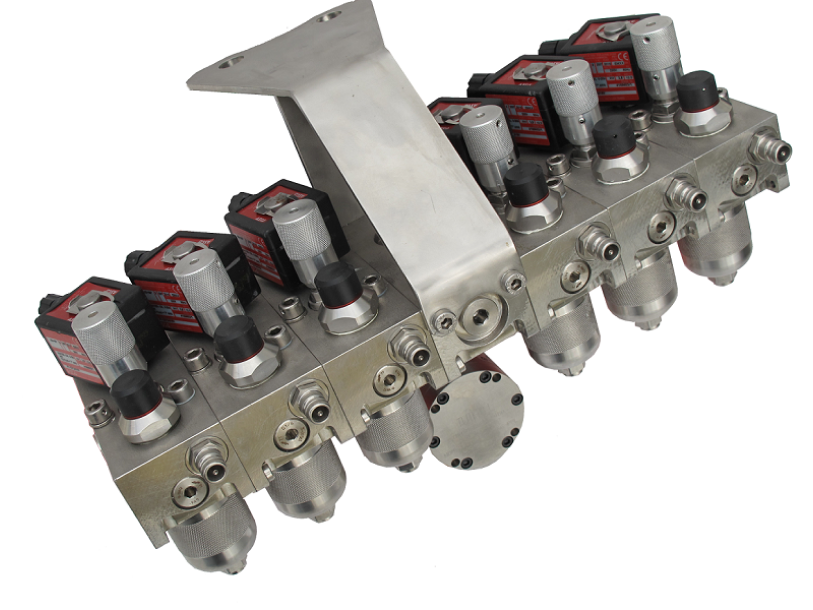
Construction of the PULSER brand additive dispenser
The PULSER additive dispenser consists of monoblocks (1) made of 316Ti stainless steel, containing:

High-capacity protective filter (sedimentation tank) with automatic contamination indicator

Shut-off solenoid valve - dosing

Throttle valve regulating the flow of the additive (with locking and sealing function)

Check valve
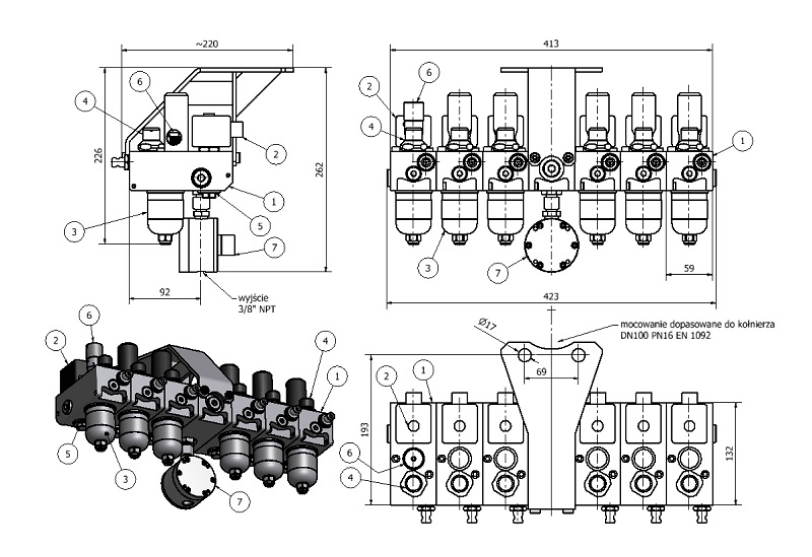
The number of monoblocks used depends on the amount of additives to be dosed. The monoblocks are connected to each other, creating a type of modular branch manifold, at the output of which one common flowmeter (7) is connected. The proprietary additives are supplied to the inputs of individual monoblocks using flexible pressure hoses equipped with quick connectors. A short section of flexible pressure hose is also used to connect the dispenser output with the technological installation of the loading station. A spray-injection valve (9) is installed on the pipeline with the base product, acting both as a non-return valve and a pressure valve, stabilising the flow. The dispenser configured in this way allows for dosing of one selected proprietary additive.

Flow meter

Spray-injection valve
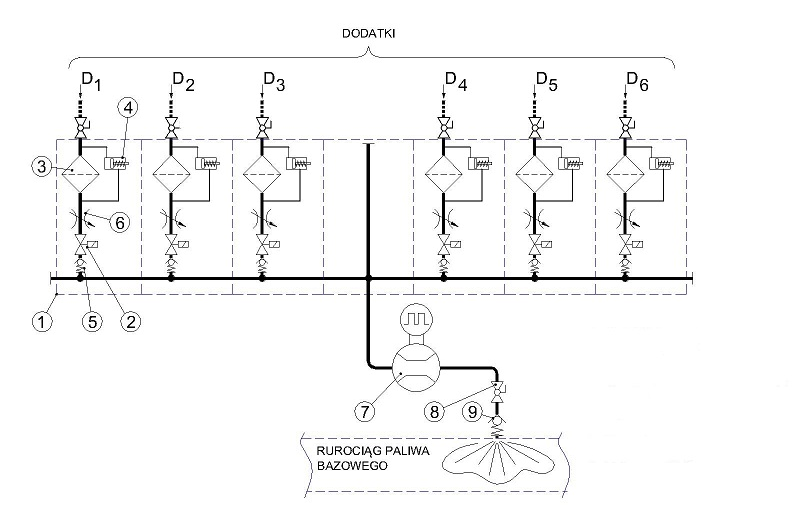
The system with one common flow meter is prepared for direct installation on the base product meter (e.g. Prime 4) in order to shorten the output connection and thus minimize the common capacities. A solution is also possible in which each of the monoblocks is equipped with an individual flow meter. In this variant, it is possible to dose several company additives simultaneously.